Refrigeration basics: A look at each step of the refrigeration cycle
*On June 1, 2023 Emerson’s Climate Technologies business became a new standalone company – Copeland. Though our name has changed, we are building on more than a century of HVACR innovation and industry leadership, and Copeland continues to offer the same products, industry stewardship, and learning opportunities you’ve grown to trust. Information found on this webpage posted before June 1, 2023 may contain our old name or branding, but you can be at ease knowing it was created with the knowledge and expertise of Copeland.
Welcome to the third installment in our blog series intended to help not just beginning service technicians, but anyone who wants to learn more about the basics of refrigeration. In this blog, I introduce some of a refrigerant system’s many basic components, explain what each is designed to do and discuss how they work together. For this blog series, we have also created companion videos that you can cross-reference while accessing other related information at Education.Emerson.com.
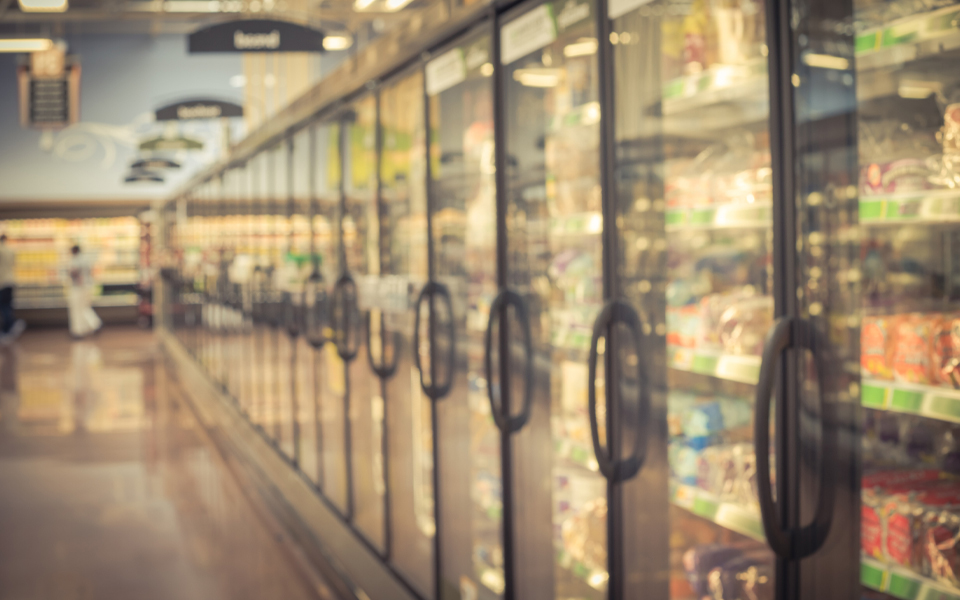
Step one: compression
In a compressor-based refrigeration or cooling system, refrigerant enters the compressor as a low-pressure, low-temperature superheated vapor and exits the compressor as a high-pressure, high-temperature superheated vapor. The compressor — which could be centrifugal, reciprocating, rotary, scroll or screw design — mechanically compresses the refrigerant gas. Under pressure, the refrigerant volume reduces, and the temperature rises.
The relationship between pressure and temperature is critical to how efficiently and effectively the system can achieve and maintain its intended setpoint.
Step two: condensing
This second step in the refrigeration process is necessary to convert the vapor to a liquid. As the compressor releases hot, pressurized refrigerant gas into a condenser, it rejects the heat by lowering or returning the temperature of the refrigerant back to its condensing temperature. Condensers utilize three primary cooling methods:
-
- Air-cooled — often found in small systems and residential applications; air flows naturally or is forced by a fan over metal (typically copper or aluminum) coils, which carry the heated refrigerant
- Water-cooled — utilized in commercial systems, large plants and when operating in higher ambient temperatures; cool water replaces natural or forced airflow around the coils carrying the heated refrigerant
- Evaporative — combines air and water cooling in large-scale facilities such as those for making ice
In most condensers, the refrigerant gas enters at the top of the equipment and leaves at the bottom because the refrigerant in a liquid state is much heavier than the weight of refrigerant in a gas state.
Step three: thermal expansion valve (TXV)
In the third step, the liquid refrigerant is cooled further when pressure is suddenly decreased by the TXV. The valve regulates the amount of refrigerant released into the evaporator in response to the cooling load.
It also measures the superheat leaving the evaporator outlet and maintains a constant temperature by raising or lowering the amount of refrigerant flowing into the evaporator. A precisely controlled flow maximizes the efficiency of the evaporator and ensures that we only have vapor returning to the compressor.
The TXV has multiple ports with bulbs that read:
-
- P1 — the temperature as refrigerant leaves the evaporator
- P2 — the pressure inside the evaporator
- P3 — the closing force to control superheat flow into the evaporator (if adjustable)
- P4 — the opening force, liquid line pressure
Step four: cooling in the evaporator
The evaporator is the part of a refrigeration system where the actual cooling takes place. In this fourth step, sub-cooled liquid refrigerant begins boiling off or vaporizes in a process that allows the refrigerant to absorb heat through a series of metal coils. The refrigerant is saturated through this process and this low-pressure, superheated vapor and then returns to the compressor to continue the refrigeration process all over.
What does a suction line accumulator do?
The last system component you should be aware of is the suction line accumulator. This device protects the compressor from a sudden surge of liquid refrigerant and oil that could enter the compressor. Compressors are designed to compress refrigerant in its vapor state. If liquid refrigerant gets into the compressor, we refer to that as “liquid floodback,” resulting in a condition called slugging that can reduce efficiency and cause premature equipment failure.
View our new video series to learn more about the refrigeration cycle. For a deeper dive into all our training content and to access our other educational resources, please visit Education.Emerson.com.
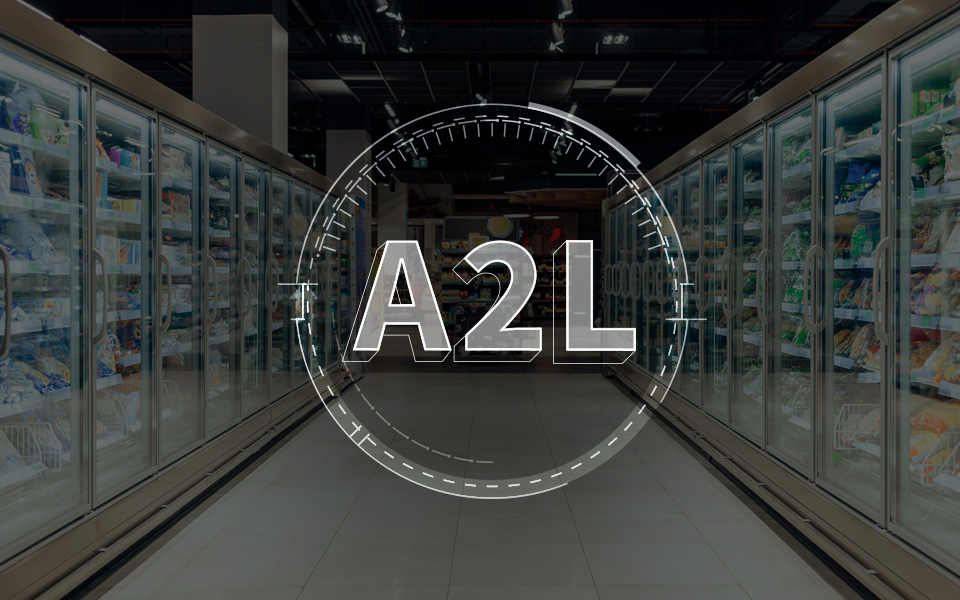
A2L Refrigeration Overview — Systems, Safety and Servicing Considerations
by Joe Summers | HVACR Industry & Tech Tips
*On June 1, 2023 Emerson’s Climate Technologies business became a new standalone company –...
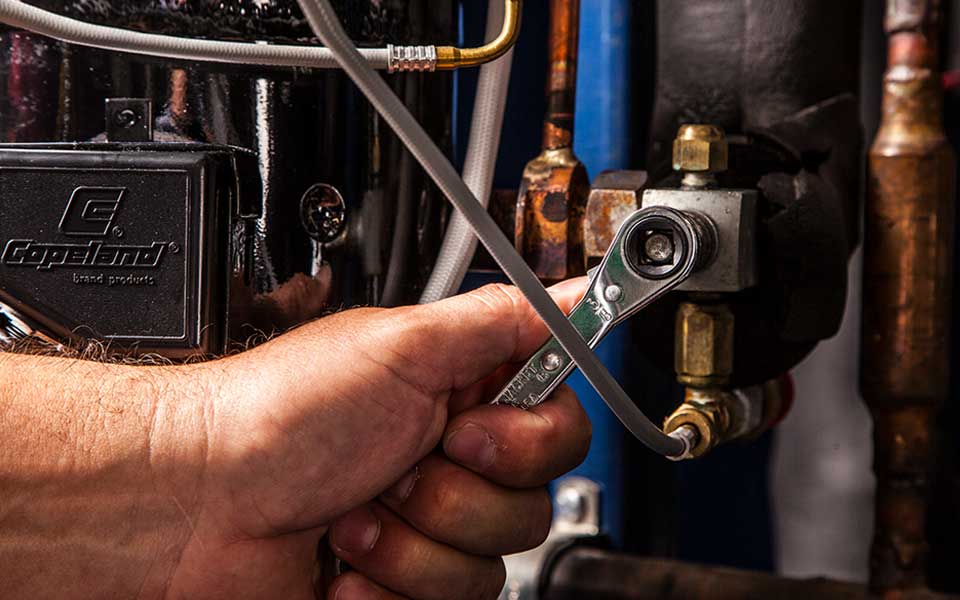
Servicing the Next Generation of Lower-GWP Refrigerants
by Joe Summers | HVACR Industry & Tech Tips
*On June 1, 2023 Emerson’s Climate Technologies business became a new standalone company –...
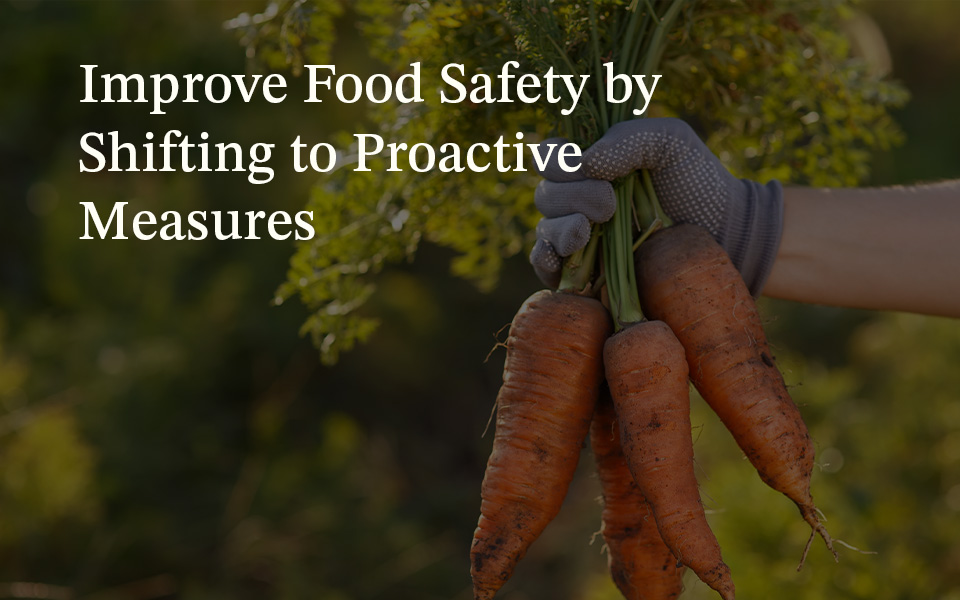
Improve Food Safety by Shifting to Proactive Measures
by Dan Knauer | HVACR Industry & Tech Tips
*On June 1, 2023 Emerson’s Climate Technologies business became a new standalone company –...
The post Refrigeration Basics: A Look at Each Step of the Refrigeration Cycle appeared first on Copeland.