Case control made simple (part 2)
*On June 1, 2023 Emerson’s Climate Technologies business became a new standalone company – Copeland. Though our name has changed, we are building on more than a century of HVACR innovation and industry leadership, and Copeland continues to offer the same products, industry stewardship, and learning opportunities you’ve grown to trust. Information found on this webpage posted before June 1, 2023 may contain our old name or branding, but you can be at ease knowing it was created with the knowledge and expertise of Copeland.
In a previous blog post, I introduced the CC200 case controller, which was recently featured in a two-part interview series on the Advanced Refrigeration Podcast. In part one of the series, we took a deeper dive into more of the technician-friendly innovations the system offers.
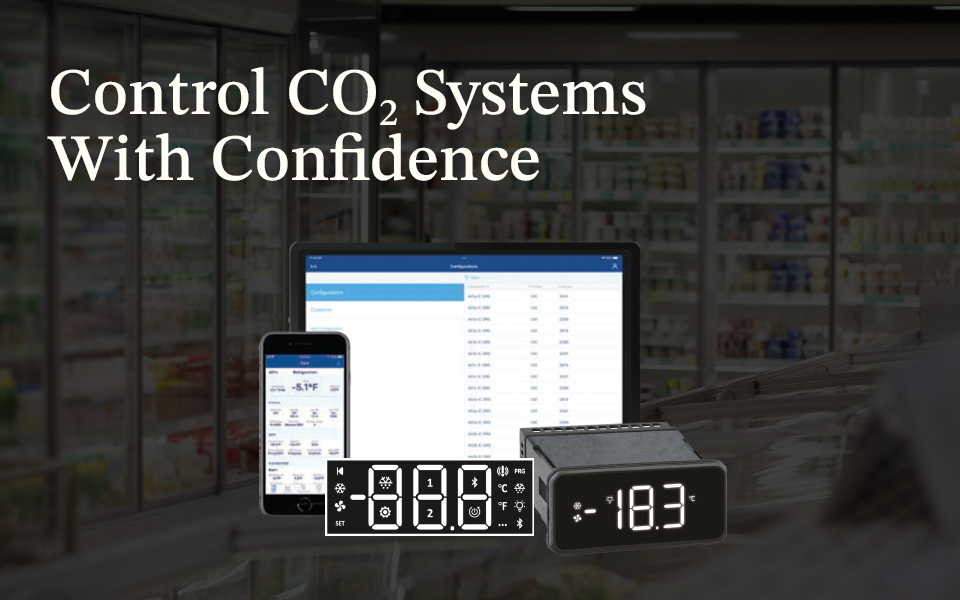
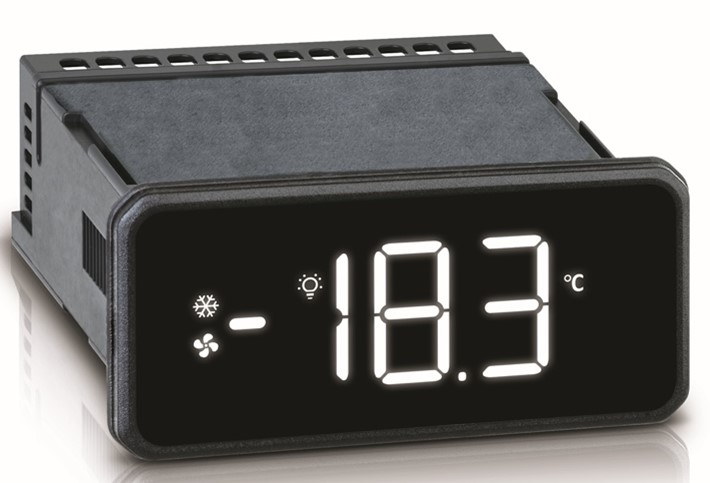
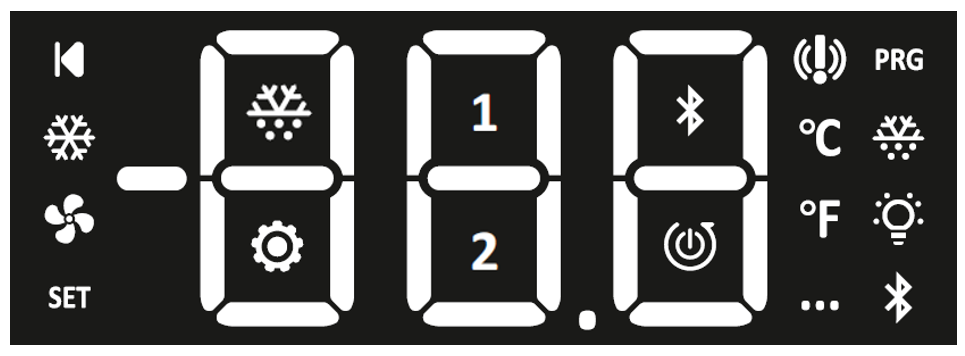
CC200 case display
Get in touch with the new case display
The CC200 case display shows temperatures and values from the CC200 controller on an LED display. It also features an easy touchscreen interface, which provides system data and intuitive navigation within the unit. Pressing and holding the upper-right corner for five seconds unlocks the display. From there you can perform quick service actions with one touch, including activating Bluetooth®, starting or stopping a manual defrost, performing a service shutdown, or rebooting the controller.
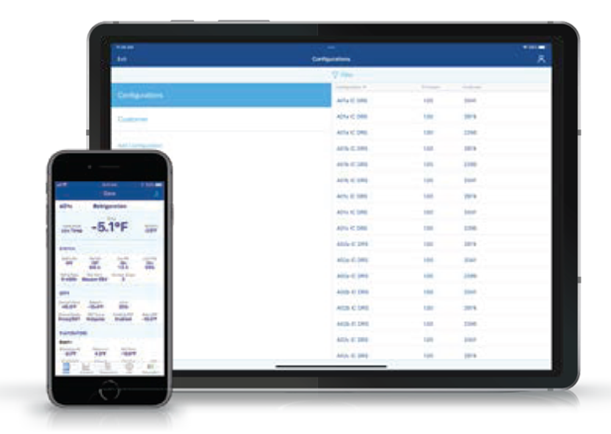
Cold Chain Connect app
Cold Chain Connect app simplifies setup and troubleshooting
Copeland’s new Cold Chain Connect mobile app provides a convenient way to connect to CC200 controllers. Cold Chain Connect is available for iOS devices from the App Store and for Android devices via Google Play. The app is designed to be a service tool that enables technicians to get started right away. Registration and approval are fast and automated, and there are no classes or additional signups required.
When you first connect to a CC200 controller, you immediately see relevant data for air temperatures, valves, evaporator superheat and suction pressure. Any active alarms are displayed in plain, descriptive language — no more time wasted looking up the meaning of three-digit codes! The app has up to 40 data points on evaporator and case operation, 12 service commands, views of all controller parameters, and access to run real-time graphs.
Technicians can easily perform manual and emergency defrosts. If you select manual defrost, the unit will follow its normal termination strategy. Emergency defrosts will run for the full duration, skipping termination. In either case, the app displays the current state of the defrost cycle in real time. Again, we made notifications as descriptive as possible. The app can also end either type of defrost at any time.
Electric valve functions such as calibration and overrides work in a similar way as defrost. And if you’ve ever used a Copeland E2E controller, you’ll probably recognize the blue color highlight that indicates an active override. The app can also be used to perform a service shutdown of CC200 — which disables all fans, valves and refrigeration for cleaning or inspection of the case.
Control CO2 systems with confidence
The CC200 provides robust case control for a variety of refrigerants including CO2. The controller also has a new EEV and superheat control algorithm with features specifically designed for CO2 refrigeration systems. The algorithm delivers precise air temperature control while maintaining a stable superheat at all times. Copeland laboratory testing and field trials of the CC200 in CO2 cases and walk-in evaporators have proven the algorithm’s performance.
The CC200 integrates seamlessly into the E3 CO2 suction group. This enables all circuit load management throughout the entire store to be performed from the suction group without the use of additional E3 flexible combiners. System startup or shutdown of case controllers is easily orchestrated from the E3 CO2 applications.
The CC200 supports multiple high-pressure ranges for the suction transducer as well as backup high-pressure alarms for startup and shutdown if the E3 should happen to be offline for any reason.
Optimize energy use with demand defrost
One of the most exciting features introduced with the CC200 is demand defrost for walk-in freezers. By running defrost cycles only when necessary, the CC200 can potentially help end users save on energy costs.
On the other hand, during periods of heavier box traffic, increased humidity or higher temperatures, the algorithm can detect when a defrost is needed and may add cycles to prevent evaporator freeze-ups (and the expensive service call to clear the ice). Integration into an E3 application can be implemented to monitor and reduce the number of simultaneous defrost cycles.
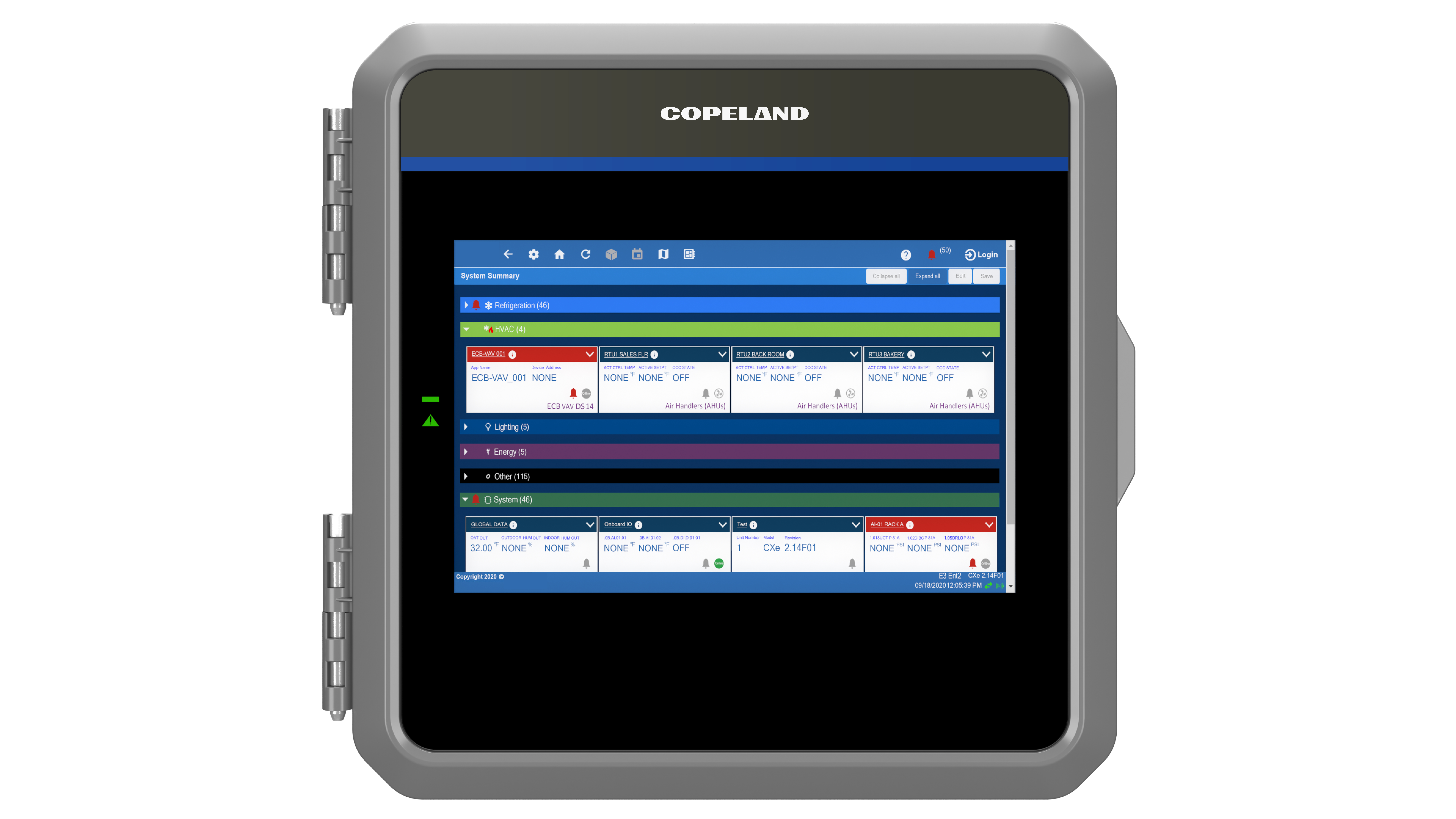
E3 controller
Seamless integration with modern supervisory controls
As noted in part one of the series, the CC200 is integrated into E2E and E3 supervisory controllers, delivering additional capabilities. In particular, the E3 enables on-site or remote access to the system in real time, providing instant visibility to all key systems, faults, status information and alarms. The E3 platform also enables control of critical systems with advanced refrigeration algorithms, building control strategies and network connectivity.
In addition to common case control functions, such as manual and emergency defrost, E3 can enable Bluetooth remotely so the unit will be ready to connect when a technician arrives at the case. Comprehensive and searchable help text is also available. The design team made extensive efforts to learn from past lessons, as well as early experiences with CO2. With E3, CO2 system control is accomplished with far fewer software applications and programming required. Core system controls — such as parallel compression, liquid or hot gas injection, oil management and management of booster systems — are easily accommodated.
If you’re suspicious about what’s going on in a particular part of the system or have a specific parameter you’re watching, the E3’s generic alarms feature enables you to create custom alarms based on any data point the system monitors. You can select high- or low-limit alarms, set limits, track state changes, and give your alarms descriptive names.
Listen and learn
The details we’ve covered in this article are just a sample of the frank and detailed discussion I had with the podcast hosts in episode two of this two-part series. Listen to the full recording to hear how the CC200 responds to specific challenges, complete with walkthroughs of the Cold Chain Connect app and E3 supervisory controller interface. For more information about the CC200 solution, including a real-world case study data and other helpful resources, visit the CC200 Case Controller webpage.
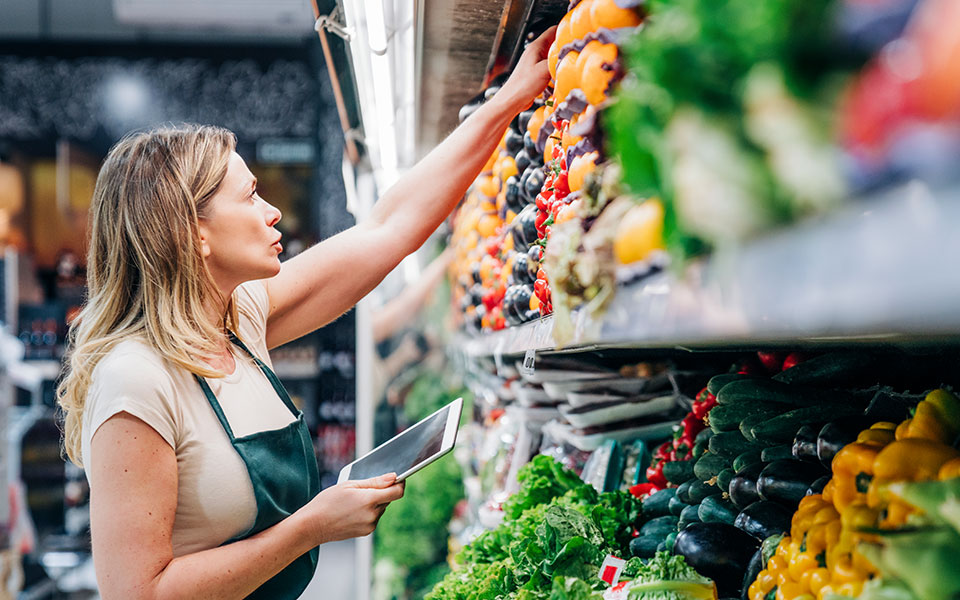
8 proven strategies for rigorous cold chain management
by Dan Knauer | Cold Chain
Preparing for the approval and safe use of A2Ls in commercial refrigeration applications...
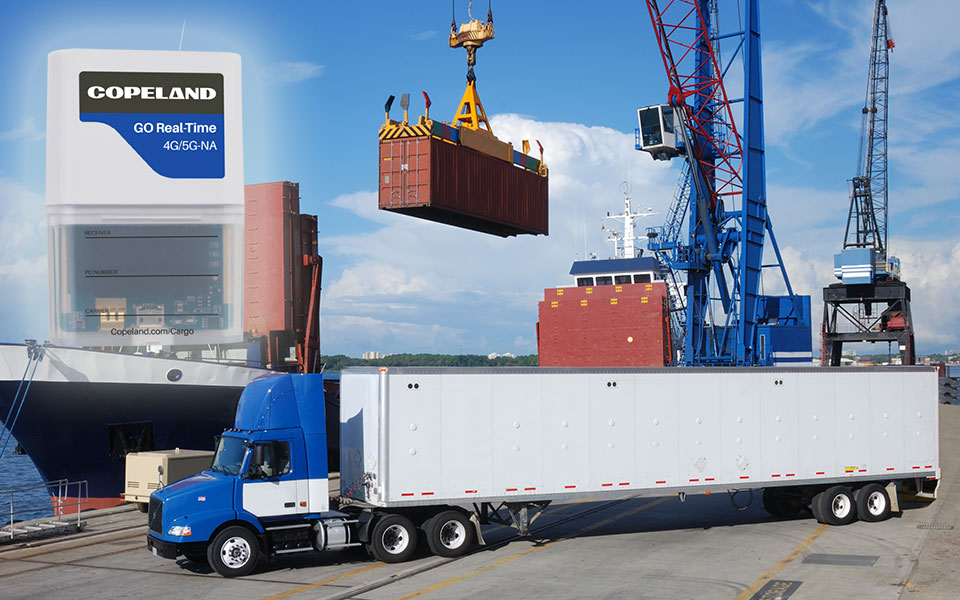
Protection for high-value shipments just got even better
by Alex Axelsson | Cold Chain, Transportation
We’re excited to announce the release of Copeland’s newest real-time tracker, the GO Real-Time...
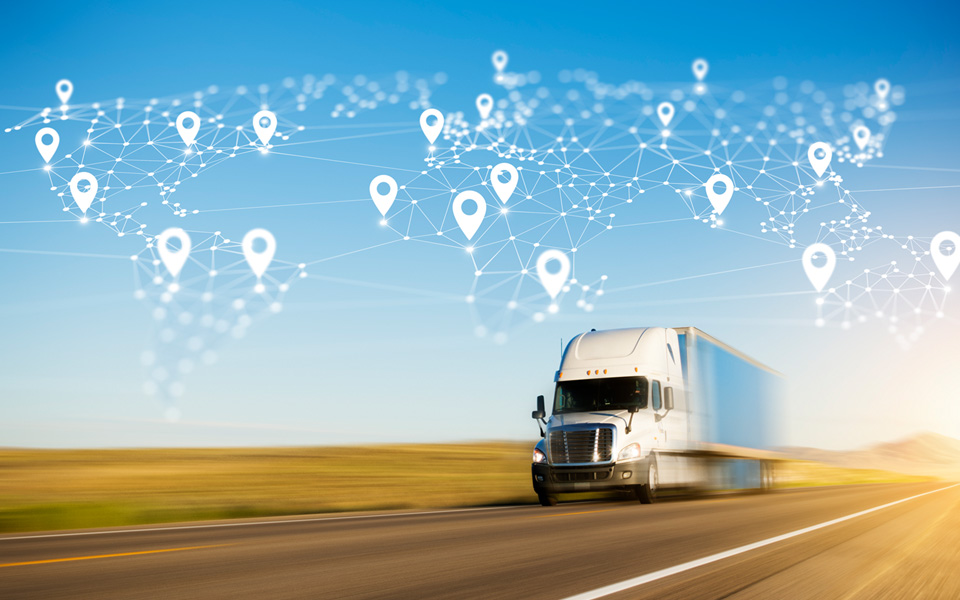
Three proven strategies to prevent cargo theft
by Chris Lafferty | Cold Chain, Transportation
The over-the-road (OTR) transport industry is experiencing a surge in cargo thefts. As thieves...
The post Case Control Made Simple (Part 2) appeared first on Copeland.