Online order volumes drive grocers to re-evaluate refrigeration strategies
*On June 1, 2023 Emerson’s Climate Technologies business became a new standalone company – Copeland. Though our name has changed, we are building on more than a century of HVACR innovation and industry leadership, and Copeland continues to offer the same products, industry stewardship, and learning opportunities you’ve grown to trust. Information found on this webpage posted before June 1, 2023 may contain our old name or branding, but you can be at ease knowing it was created with the knowledge and expertise of Copeland.
As I discussed in a previous blog, the coronavirus pandemic forced many food retailers to shore up their click-and-collect fulfillment capabilities to meet consumer demand for an in-store shopping alternative. While many shoppers tried click-and-collect for the first time during the early phases of the pandemic, industry experts expect this change in buying habits to continue well into the future. In a recent ACHR News article, I explored further how grocers are adapting their refrigeration strategies to support an increased volume of click-and-collect orders.

With the onset of the pandemic and the precipitous rise in online fulfillment, many grocers scrambled to add refrigerated areas to stage their customers’ fresh and perishable orders. Months later, the impacts of the lingering pandemic continue to be felt throughout the cold chain — from food retail to distribution and warehousing strategies. For many grocery supply chain stakeholders, this is an opportunity to deploy innovative technologies that they had only thought about implementing previously.
Explore new distribution warehouse strategies
The grocery industry had been experiencing growth in distribution warehouse infrastructures well before the pandemic; with increased e-commerce fulfillment requirements, we expect this trend to accelerate. As part of their efforts to support click-and-collect fulfillment, many retailers are experimenting with various store formats, including dark stores, micro-fulfillment centers (MFCs) and automated warehouses.
In many cases, existing store layouts are not ideally or efficiently designed to handle large amounts of online orders, and having employees on the sales floor picking to fulfill orders can disrupt the in-store shopper experience. To alleviate these emerging pressures, we may see more MFCs and dark stores dedicated exclusively to the fulfillment of online orders.
Implement food safety and environmental controls
As retailers integrate more of these types of fulfillment facilities to improve efficiencies in their picking and order consolidation processes, ensuring food safety will become increasingly important. There’s no question that the pandemic has created renewed focus on grocers’ efforts to protect the health and safety of employees, customers and of course, food. As part of this focus, grocers are evaluating various tools and technologies to help them monitor and control equipment and systems so that their employees can concentrate on providing positive customer experiences.
This will likely translate into a greater demand for critical control systems that help grocers achieve food safety- related objectives, including:
-
- Identifying key refrigeration and facility performance issues
- Implementing periodic air changes (refreshes)
- Keeping food safe and sanitary
The abilities to perform remote monitoring, troubleshooting and problem resolution — including predictive failure and maintenance analysis — are becoming essential resources for retailers hoping to schedule service intervals and minimize disruption to in-store shoppers. Grocers can also leverage these tools and technologies to implement a variety of other key store activities, such as: enabling connected, hand-washing stations for increased sanitation; installing remote, wireless sensors for food quality monitoring; or providing enhanced HVAC controls to help maintain indoor air quality.
Consider sustainable refrigerant alternatives
As grocers adapt to the consumer preference for click-and-collect fulfillment, many face the prospect of remodeling their stores to supply this additional refrigeration load. This will give them a prime opportunity to transition toward alternative refrigerants with lower global warming potential (GWP).
Many retailers have considered beginning this transition for quite some time but were uncertain about when to start the process. From a timing perspective, it may make sense to start aligning new store design upgrades with their future refrigerant and sustainability objectives. And in certain areas of the country — where grocery demand may be returning to pre-pandemic levels — many retailers will be well-positioned to invest in new refrigeration equipment or store upgrades.
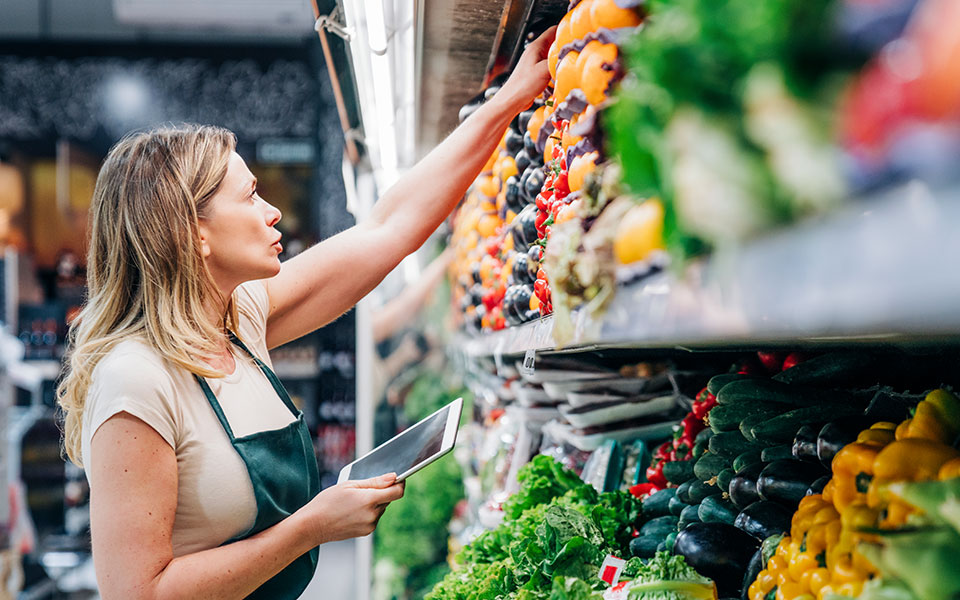
8 proven strategies for rigorous cold chain management
by Dan Knauer | Cold Chain
Preparing for the approval and safe use of A2Ls in commercial refrigeration applications...
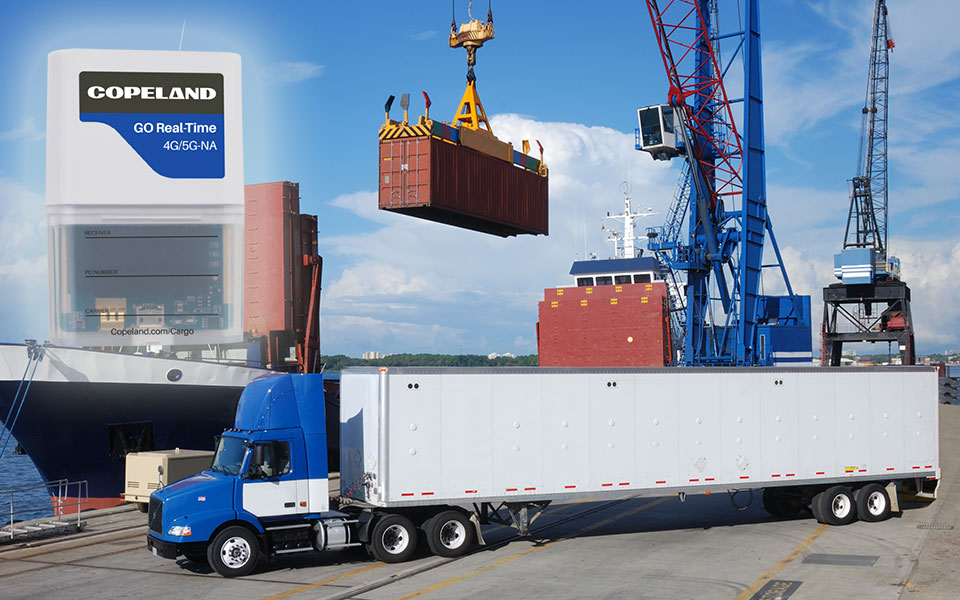
Protection for high-value shipments just got even better
by Alex Axelsson | Cold Chain, Transportation
We’re excited to announce the release of Copeland’s newest real-time tracker, the GO Real-Time...
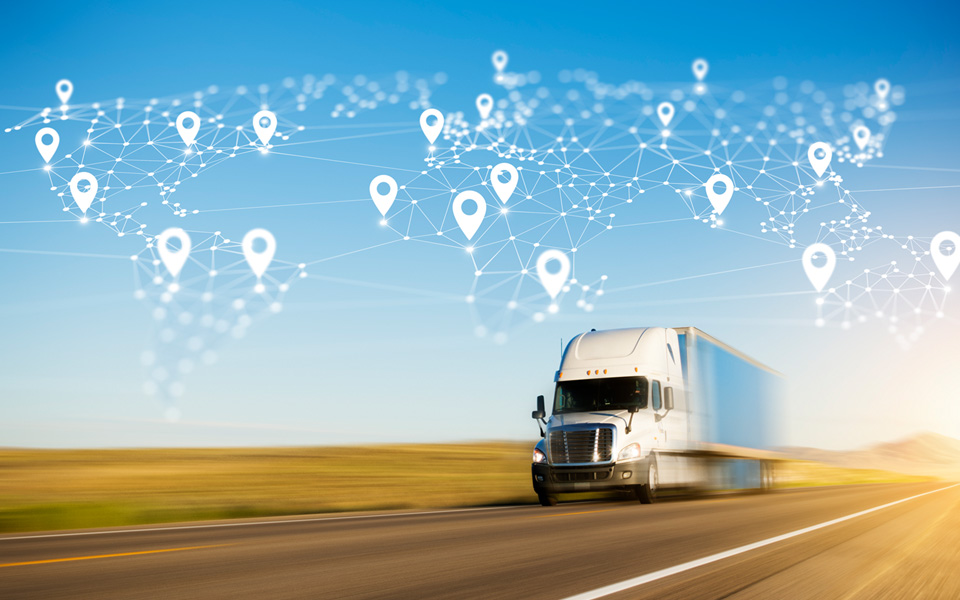
Three proven strategies to prevent cargo theft
by Chris Lafferty | Cold Chain, Transportation
The over-the-road (OTR) transport industry is experiencing a surge in cargo thefts. As thieves...
The post Online Order Volumes Drive Grocers to Re-Evaluate Refrigeration Strategies appeared first on Copeland.