10 innovations transforming retail operations
*On June 1, 2023 Emerson’s Climate Technologies business became a new standalone company – Copeland. Though our name has changed, we are building on more than a century of HVACR innovation and industry leadership, and Copeland continues to offer the same products, industry stewardship, and learning opportunities you’ve grown to trust. Information found on this webpage posted before June 1, 2023 may contain our old name or branding, but you can be at ease knowing it was created with the knowledge and expertise of Copeland.
Exploring emerging solutions to the HVACR industry’s biggest challenges
Deadlines are rapidly approaching for new regulations and proposals that are spearheading the transition to lower-global warming potential (GWP) refrigerant substitutes. Next-generation alternatives like A2Ls, A3s and CO2 will become increasingly commonplace as the hydrofluorocarbon (HFC) phasedown progresses over the next several years.
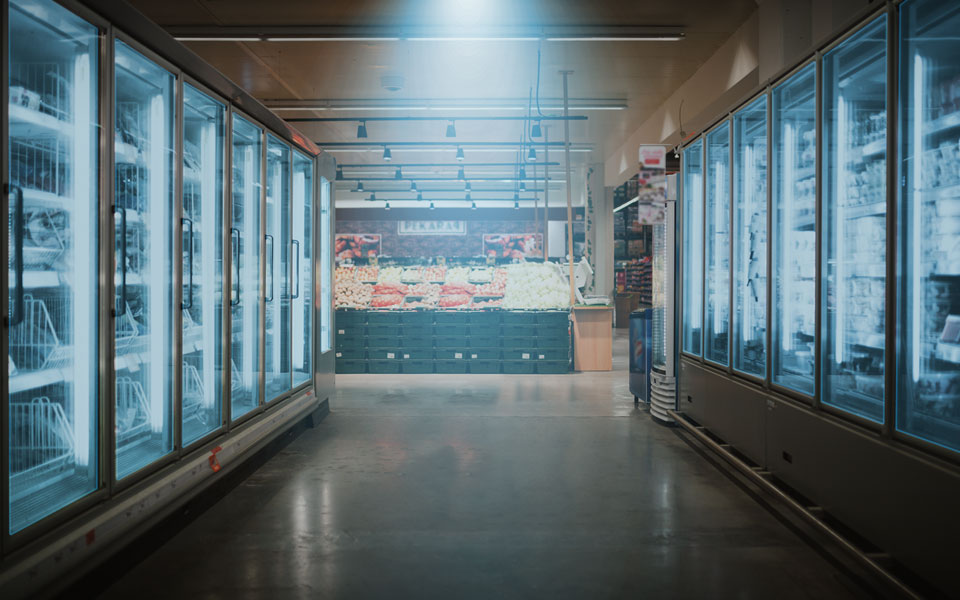
New equipment and refrigerants will pose steep learning curves for service technicians. As the refrigerant transition continues to transform the equipment supply chain, emerging solutions must be tailored to help simplify it and enable remote visibility into retail customers’ systems.
Significant research and development (R&D) are underway to address these converging challenges. In a recent article for Progressive Grocer, I outlined 10 innovations that are poised to transform the future of retail operations.
- Refrigerant leak detection
Leak detection will be essential for ensuring safety in flammable A3 and lower-flammability A2L refrigerants. It will also become even more important in existing equipment to limit HFC emissions and preserve refrigerant charges. Integrated leak detection and case control solutions will improve safety, temperature precision, system performance and efficiency.
- Demand response and load shifting
Energy optimization programs offered by local utilities can help retailers mitigate peak demand charges and lower annual electricity costs. Connected energy management controls are necessary for participation in several of these initiatives, including grid-interactive building (GEB) and distributed energy resource (DER) programs. Optimization strategies that leverage AC rooftop units (RTUs) or lighting controls, rather than focusing on refrigeration, offer approaches which remove concerns about food quality and safety.
- Cold thermal energy storage (CTES)
CTES technology primarily targets frozen or low-temperature (LT) loads, which present lower risks to food quality and safety. LT freezer setpoints are lowered during low demand periods. Then, during peak periods, the thermal energy of the frozen food helps maintain temperatures with less electricity, lowering (or avoiding) peak charges. Battery back-ups can be used in a similar fashion to assume the electrical load of a refrigeration footprint during brief periods of peak demand.
- Integrated compression and controls
Connected controls can continually evaluate system variables and maximize efficiency — without impacting reliability. In this way, they can push compressors to their pressure limits when maximum capacity is needed while optimizing performance in the lower range.
- Variable frequency drives (VFDs) in commercial refrigeration
Advancements in VFD and scroll compressor integration are overcoming historic challenges, enabling lower energy consumption, multiplexing configurations in remote condensing units, precise load matching and increased reliability.
- Autonomous system control
The need for CO2-specific rack and system controls has driven the advancement of autonomous controls that will help end users and service technicians with all types of refrigeration technologies. Connected ecosystems combine system controls, case controllers, leak detection and associated devices to enable deep visibility into system performance and operation.
- Smaller-footprint, distributed CO2 refrigeration
CO2 booster systems and compression technologies are evolving to support smaller, more centralized refrigeration strategies and even individual condensing units. Distributed CO2 systems will also help support end-of-life equipment strategies, enabling sections of legacy systems to be phased out in favor of low-GWP, CO2 refrigeration technologies.
- Climatic optimization of CO2 booster systems
Historically, base CO2 booster systems have been more efficient in cooler climates than in warmer regions. But modern climate-specific optimization strategies are closing the gap. A recent climate study commissioned by Copeland evaluated leading design strategies, providing recommendations based on climatic conditions.
- Adiabatic (wet) gas coolers improve efficiencies in hot, dry climates.
- Parallel compression is most effective in hot, high-humidity climates, providing higher annual energy savings than adiabatic gas coolers in regions where the humidity is above 30 percent.
- Low to zero superheat delivers annualized energy efficiency gains, regardless of climatic conditions.
- Wider adoption of flammable refrigerants
The imminent EPA approval of A2Ls and higher charges of R-290 in self-contained equipment are driving innovations in system safety. Mildly flammable A2Ls will require optimized components but are expected to fill a broad niche of self-contained and remote systems. Although R-290 is already widely used, charges are currently restricted to 150 grams. Higher charges up to 500 grams will significantly increase system capacity and the breadth of potential applications.
- Scope 3 emissions tracking
Although Scope 1 (direct) and Scope 2 (indirect) emissions are the targets of many current innovations, companies are also evaluating how their supply chains can help them meet Scope 3 (lifecycle climate impacts) targets for greater sustainability gains.
Preparing for the future of refrigeration
As the refrigerant transition continues to transform the equipment supply chain, Copeland is working closely with our original equipment manufacturer (OEM) partners to help them develop technologies that address modern retail challenges. Emerging solutions are designed to simplify installation, commissioning and operation of lower-GWP refrigeration technologies — with the goals of helping end users and service technicians to better manage the ongoing, industry-wide transition.
To support OEM product developmental efforts and address escalating retail challenges, Copeland has assembled a cross-functional group of internal subject matter experts (SMEs) with more than 450 years of collective HVACR experience. The Copeland Solutions Teams lends its expertise and support services to customer projects, market research and solutions ideation.
As HVACR industry stakeholders encounter unexpected roadblocks along the journey ahead, the Copeland Solutions Team will work to solve the industry’s most pressing technological challenges. To learn more about current and upcoming solutions, read the full article.
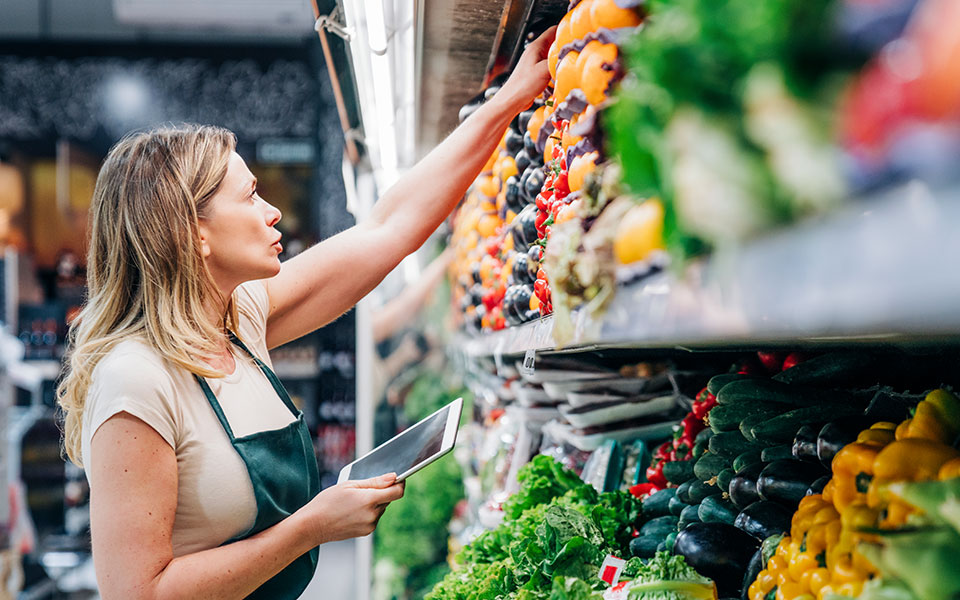
8 proven strategies for rigorous cold chain management
by Dan Knauer | Cold Chain
Preparing for the approval and safe use of A2Ls in commercial refrigeration applications...
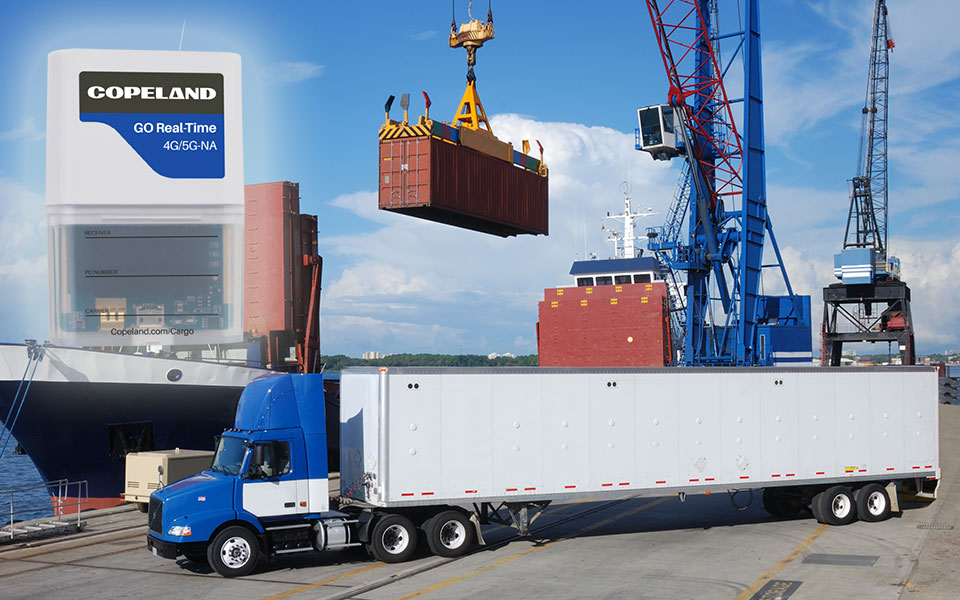
Protection for high-value shipments just got even better
by Alex Axelsson | Cold Chain, Transportation
We’re excited to announce the release of Copeland’s newest real-time tracker, the GO Real-Time...
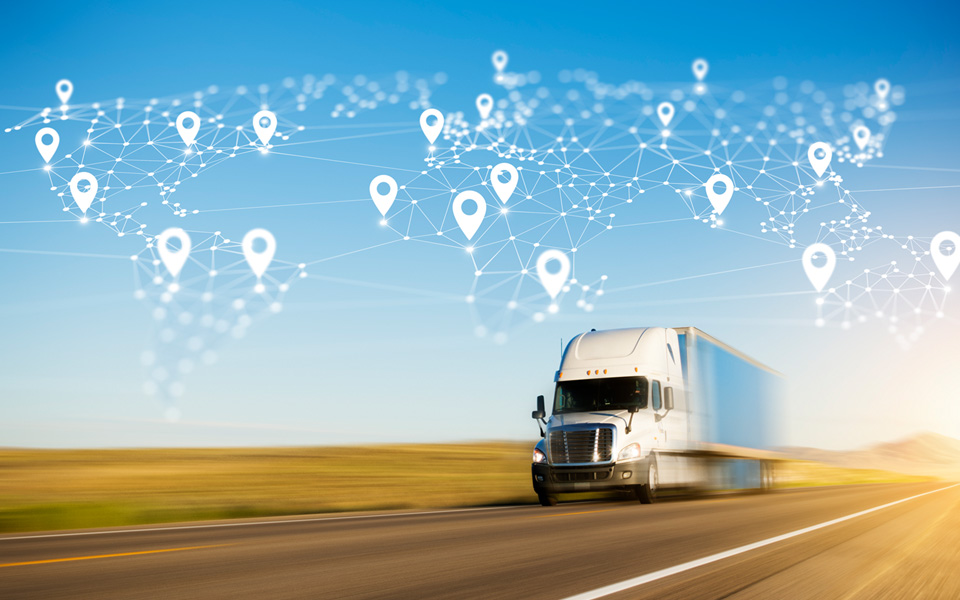
Three proven strategies to prevent cargo theft
by Chris Lafferty | Cold Chain, Transportation
The over-the-road (OTR) transport industry is experiencing a surge in cargo thefts. As thieves...
The post 10 Innovations Transforming Retail Operations appeared first on Copeland.