Simplify refrigerated case servicing and troubleshooting
*On June 1, 2023 Emerson’s Climate Technologies business became a new standalone company – Copeland. Though our name has changed, we are building on more than a century of HVACR innovation and industry leadership, and Copeland continues to offer the same products, industry stewardship, and learning opportunities you’ve grown to trust. Information found on this webpage posted before June 1, 2023 may contain our old name or branding, but you can be at ease knowing it was created with the knowledge and expertise of Copeland.
Effective troubleshooting is a fundamental skillset for service technicians responsible for keeping refrigerated cases running at peak performance. They need tools to help them quickly set up new cases and diagnose issues in existing units — stabilizing air temperatures, superheat and defrost schedules — all while minimizing in-store disruptions. The Copeland CC200 case controller was designed with these priorities in mind. In the last blog of our Innovations in Case Control series, I review how its powerful combination of software, hardware and mobile app provides a robust collective toolset for simplifying every aspect of servicing and troubleshooting.
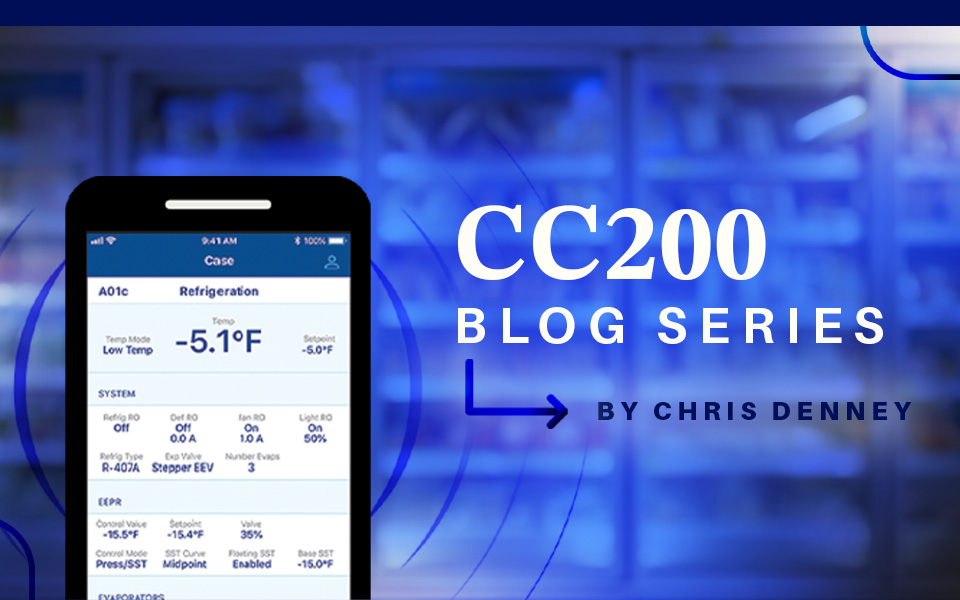
Connect to full visibility and control
Designed for seamless integration of software, hardware and a dedicated mobile app, the CC200 case controller enables full visibility to case status and key performance metrics. Bluetooth connectivity places this information into technicians’ hands via the Cold Chain Connect mobile app, which is free and available on both Apple and Android platforms.
With the Cold Chain Connect app installed, a technician can walk into a store, locate the case in question, and This connected convenience saves technicians from having to locate a supervisory controller — which could be on the roof or at the compressor rack. Suction pressure, superheat, evaporator coil outlet temperature, fan motor amperage and many more data points are available — without removing food or shelving from the case to investigate.
Technicians can access the Cold Chain Connect app and begin troubleshooting within minutes:
- Review active alarms and setpoints
- Access more than 40 data points
- View real-time graphs to visualize data trends
- Initiate key override service commands
- Quick access to CC200 documentation and wiring guidelines
With the Cold Chain Connect app, technicians have all the data they need to diagnose issues or simply check case operation. It’s never been easier to handle common service scenarios.
One controller for multiple case designs and configurations
As I had covered in previous blogs, the CC200 case controller hardware is designed for use with optional expansion modules to control up to three evaporators or an electronic evaporator pressure regulator (EEPR) valve. Easy-to-use expansion port connectors simplify refrigerated case installation, enabling each expansion module to leverage the power source and communication capabilities from the main controller.
The CC200 case controller enables the flexibility to handle multiple applications and components, including: stepper-motor electronic expansion valves (EEVs), pulse width modulated (PWM) expansion valves and EEPR valves. Other flexible features are support for low-, medium- and dual-temperature case designs, multiple lower-GWP refrigerants (including CO2) and up to three evaporators per case controller. This gives technicians a common, familiar device for all cases, while providing original equipment manufacturers (OEMs) with one controller platform for multiple case designs.
Software on the CC200 case controller is engineered to help technicians stabilize performance. Advanced control algorithms automatically and continuously fine-tune superheat, case temperatures, case pressures and all control functions needed for optimized case control. The CC200 can be used as a stand-alone controller or seamlessly integrated with the E3 supervisory control, easily adapting to the control infrastructure of each retail scenario.
These robust capabilities have been lab-tested and field-proven in pilot tests and a growing number of installations throughout the U.S.
Built-in OEM support
The CC200 case controller and its Cold Chain Connect app feature an additional toolset built specifically for OEMs and their field technicians. The parameter configuration feature enables OEMs to create for each of their case designs and store them in the Cold Chain Connect app’s cloud infrastructure for future use.
This makes parameters readily available for factory personnel to download wirelessly into the controller with the Cold Chain Connect app. And when Copeland releases new firmware for the CC200 case controller, all saved configurations will be upgradeable to latest firmware version.
OEMs can also take advantage of the app’s factory test mode, which allows them to fully test the CC200 case controller’s integration with a case before it leaves the factory. This mode includes a guided test procedure that checks sensor, valve, relay and defrost operations. After the test mode is concluded, the app automatically generates a PDF report that can be exported and shared.
To learn more about the CC200 case controller’s many servicing, troubleshooting, installation and start-up features, please view our companion video series.
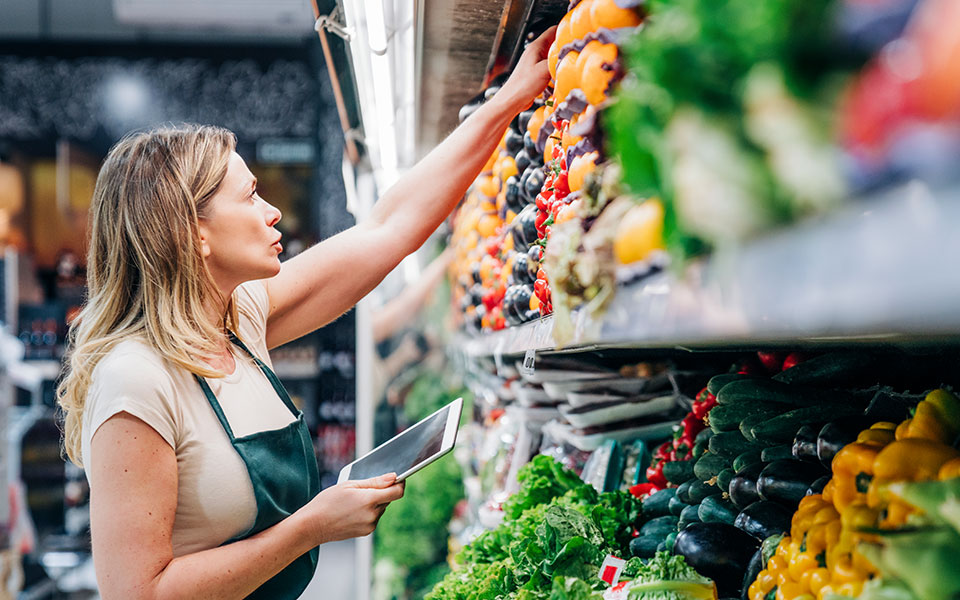
8 proven strategies for rigorous cold chain management
by Dan Knauer | Cold Chain
Preparing for the approval and safe use of A2Ls in commercial refrigeration applications...
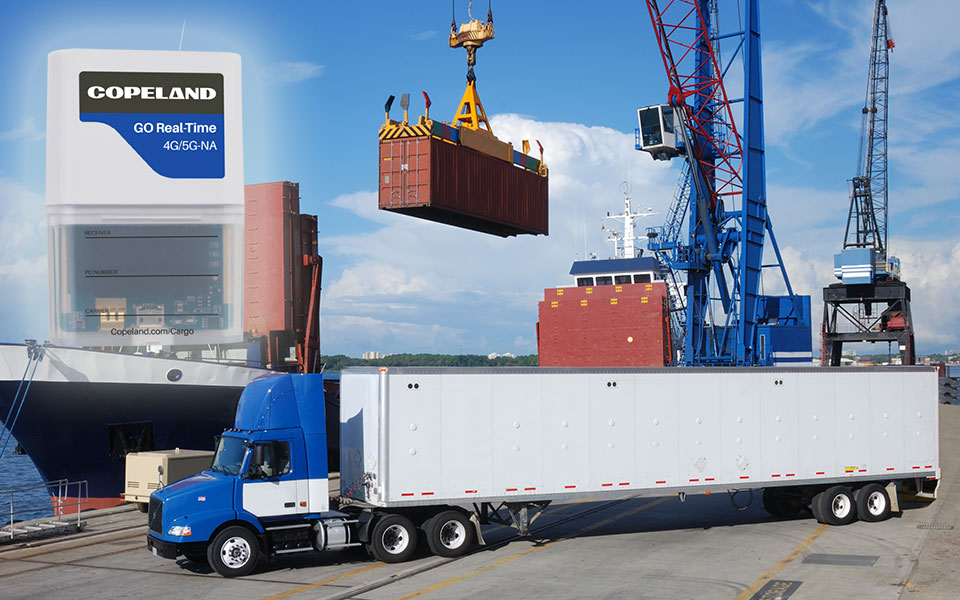
Protection for high-value shipments just got even better
by Alex Axelsson | Cold Chain, Transportation
We’re excited to announce the release of Copeland’s newest real-time tracker, the GO Real-Time...
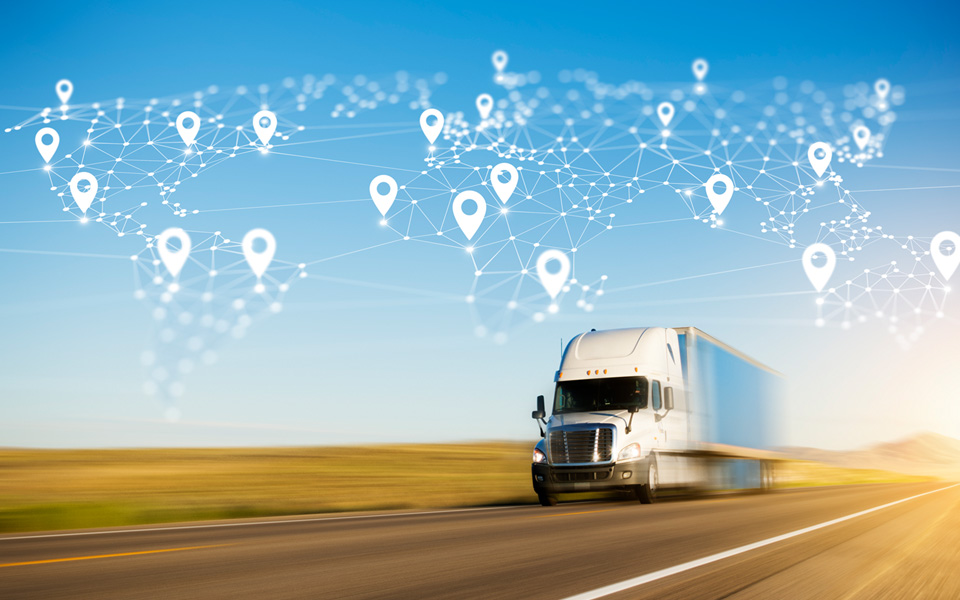
Three proven strategies to prevent cargo theft
by Chris Lafferty | Cold Chain, Transportation
The over-the-road (OTR) transport industry is experiencing a surge in cargo thefts. As thieves...
The post Simplify Refrigerated Case Servicing and Troubleshooting appeared first on Copeland.