CO₂ as a refrigerant – selecting a best-fit system for your operation

For the final post of our CO2 as a Refrigerant blog series, I examine which CO2 system architectures are best suited for different retail scenarios and review emerging strategies for improving energy efficiencies.
By far, the most common CO2 refrigeration system used in global food retail applications is the CO2 booster architecture — also referred to as a CO2 transcritical booster system. A CO2 booster system is ideal for retailers with large facilities who are seeking a centralized, all-CO2 strategy for both medium- (MT) and low-temperature (LT) loads. Although CO2 booster refrigeration has been used for more than two decades, recent technological advancements — and improvements in integrated system controls strategies — have greatly simplified system installation, commissioning, servicing and daily operation. In addition, centralized CO2 booster systems are evolving to accommodate smaller facility sizes and applications.
CO2 cascade systems have emerged as an alternative to CO2 booster systems in warm-climate supermarket and/or chiller applications, using a combination of CO2 and hydrofluorocarbon (HFC) refrigerants. This architecture consists of two distinct refrigeration circuits: a CO2 circuit for the LT suction group and an HFC refrigerant for the MT circuit — designed to keep the CO2 side of the system operating only in subcritical mode. Today, lower-global warming potential (GWP) HFCs or A2L refrigerants are being used on the high side of systems.
As CO2 condenses in the LT circuit, heat discharges (i.e., cascades) into the MT suction stage via an intermediate heat exchanger designed to always keep the LT CO2 stage in subcritical mode (i.e., below 87.8 °F) MT compressors send the lower-GWP HFC refrigerant to an air-cooled condenser on the roof, much like a typical HFC system.
Continued advancements in CO2 compression technology are supporting the emergence of distributed, CO2 single-stage (MT) refrigeration. Restaurants, convenience stores and small-format retailers who currently use MT condensing units (CDUs) and mini-rack systems for walk-ins and display case line-ups will soon have the option to use these flexible CO2 options in the U.S.
Distributed CO2 systems are already installed in Europe, where Copeland has launched its CO2 transcritical scroll compressor. Our North American launch will take place in 2024, when these small, sustainable CO2 refrigeration systems will be introduced to U.S. markets. Even for larger retailers seeking end-of-life HFC equipment strategies, distributed CO2 systems provide a gradual means to phase out underperforming sections of HFC direct expansion (DX) systems and start the process of phasing in CO2 CDUs or mini-racks.
CO2 booster optimization for warm climates
CO2 booster systems originally emerged in cooler climates where low ambient temperatures prevent the system from running in a supercritical operation. But the refrigerant transition has driven the need for sustainable CO2 system options in all climates. Manufacturers have developed optimization technologies designed to improve CO2 system performances and efficiencies in warm or hot annual and/or peak temperatures.
- Dry gas cooler for cold, dry climates
- Dry gas cooler plus parallel compression for climates above 30 percent humidity
- Adiabatic (wet) gas cooler for hot, dry climates
Retailers can leverage these optimization strategies to achieve the lowest total cost of ownership (TCO) in each store location. For example, by evaluating local utility costs, electricity rates and water availability, retailers can align an optimization strategy for the local climate to reduce lifecycle costs. Considering that monthly electricity rates are often driven by peak consumption periods, retailers with installations in high-cost kW/hr regions should do everything possible to minimize high peak usage — even if peak usage only occurs for a few days out of a typical year.
For retailers exploring CO2 boostersystems for store installations or retrofits, Copeland recently completed a CO2 climate study that provides third-party analysis on how to select a system optimization strategy. By leveraging Copeland’s integrated CO2 compressors, controls and system components, we’re helping retailers maximize energy efficiencies and achieve the lowest TCO in every climate.
This concludes our CO2 as a Refrigerant blog series. To learn more about climate impacts on CO2 systems and explore the expanding potential of CO2 refrigeration, please visit our content hub.

Six Ways to Reduce Food Waste by Tracking the Supply Chain
by Gerd Uitdewilligen | Cold Chain
*Emerson’s Climate Technologies business is now a new standalone company: Copeland. Over the next...
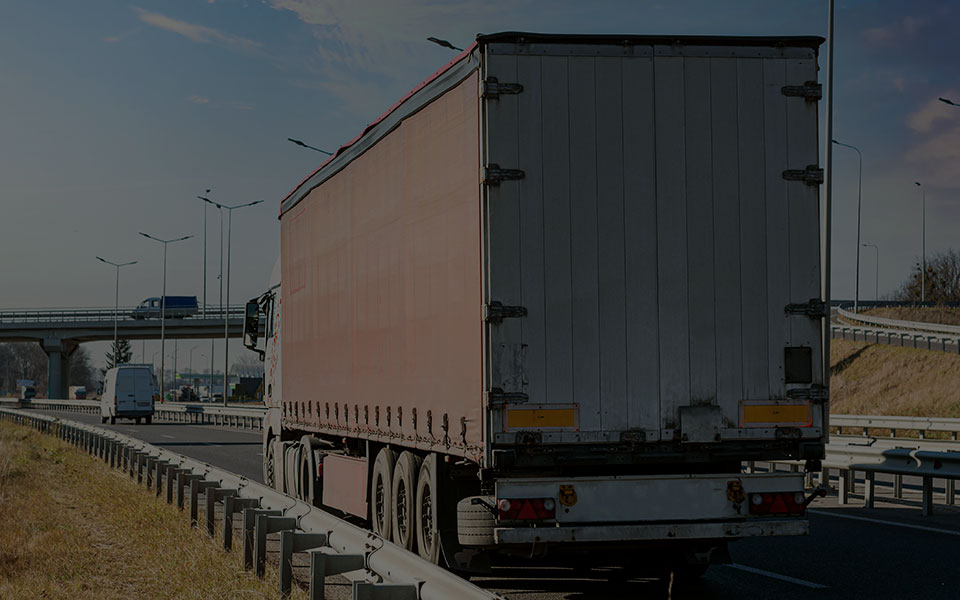
Protect Valuable Shipments in High-Crime Areas
by Lissandra Rodriguez | Cold Chain
*Emerson’s Climate Technologies business is now a new standalone company: Copeland. Over the next...
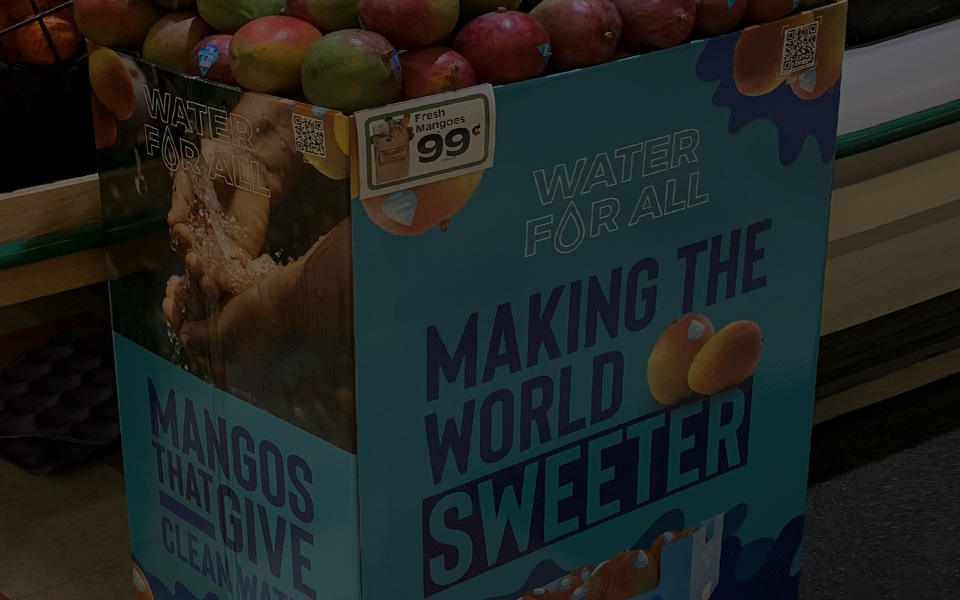
Real-time Tracking Protects Valuable Mango Cargo
by Andres Toro | Cold Chain
*Emerson’s Climate Technologies business is now a new standalone company: Copeland. Over the next...
The post CO2 as a Refrigerant – Selecting a Best-Fit System for Your Operation appeared first on Copeland E360 Blog.