Optimize supermarket energy efficiency and performance with VFD retrofits
*On June 1, 2023 Emerson’s Climate Technologies business became a new standalone company – Copeland. Though our name has changed, we are building on more than a century of HVACR innovation and industry leadership, and Copeland continues to offer the same products, industry stewardship, and learning opportunities you’ve grown to trust. Information found on this webpage posted before June 1, 2023 may contain our old name or branding, but you can be at ease knowing it was created with the knowledge and expertise of Copeland.
The use of fixed-speed (or fixed-capacity) refrigeration systems and HVAC rooftop units (RTUs) is a common strategy in the U.S. food retail sector. If you went into the machine rooms of most grocery stores, you likely would find centralized, direct expansion (DX) refrigeration systems with parallel racks of fixed-speed compressors. On the rooftops, you would find RTUs with air-handler blowers running continuously at full speeds. Varying the capacity of these critical units relies on mechanical throttling techniques that consume energy, cause excess equipment wear, but never quite achieve the desired load matching. In a new white paper, Emerson explore how operators can retrofit these systems with variable frequency drives (VFDs) to deliver significant energy efficiency and performance improvements.

-
- Reduced energy consumption and electricity costs
- Improved load matching, temperature precision and performance
- Extended equipment reliability lifespan
VFDs in refrigeration systems
The inability to match the refrigeration capacity to fluctuating evaporator load demands is a known limitation of parallel rack systems with fixed-speed compressors. Systems are designed and specified to accommodate peak-load conditions and provide reliable cooling during the hottest days of a year — i.e., they’re essentially over-sized for lower load conditions and cooler periods.
Widely varying load requirements, ever-changing ambient conditions and variations in defrost cycles can create undesirable fluctuations in case temperatures. Compressors are constantly switching off and on to try and adapt to these changing demands, which can accelerate wear on system components, increase the potential for food quality issues, and consume excess electricity.
VFDs give operators and service technicians an effective method for alleviating fixed-speed compressor motor challenges and achieving the benefits of variable-capacity modulation. By retrofitting a VFD to the lead compressor in every parallel compressor rack, each lead compressor can then modulate the capacity of the entire rack. This enables fixed-speed compressors to handle the base load, while leveraging the VFD-equipped lead compressor to manage fluctuations in demand. Compared to a traditional fixed-speed approach, this results in:
- Reduced cycling on/off strain and an extended life of the lead compressor
- Smoother and almost constant system suction pressure
- More consistent evaporator (case) temperatures and humidity conditions
Validating VFD ROI in HVAC case study
In HVAC RTUs, air-handler blower capacity is also designed to handle the peak cooling conditions of the installation’s summer season. But as building loads fluctuate widely throughout the year, HVAC systems often operate at only a fraction of their design capacity. Thus, air-handler blower fans run continuously at full, fixed speeds, regardless of load requirements. Technicians often use a mechanical throttling technique to help reduce airflow, but this results in increased energy consumption and a reduction in the equipment’s lifespan.
Retrofitting a VFD onto an existing fan motor allows it to modulate capacity based on varying load requirements — full speed during peak-load periods and slower speeds when less load is required. In this HVAC RTU application, variable-capacity modulation delivers a fast return on investment (ROI) via a non-linear, speed-to-power ratio. By slowing down a blower motor fan speed by 25 percent of its normal operating rate, it’s estimated that facility operators can reduce energy consumption by 50–60 percent.
Emerson validated this principle recently by installing Copeland™ VFDs on a food retailer’s existing rooftop HVAC air-handler blower motors in 78 of their stores. Results included:
- Reduced energy consumption by 52 percent
- Saved more than $800,000 in electricity costs
- Equivalent to adding $10M in sales at an 8 percent margin
Retrofit with Copeland VFDs
Emerson is committed to helping food retailers and technicians to simplify the retrofit process in HVACR applications and improve equipment reliability, performance and efficiency. Copeland VFDs, EVM/EVH Series are designed to reduce the costs and complexities of VFD implementation:
- The Copeland EVM Series is ideal for chillers, medical refrigeration, display cases, walk-ins and reach-ins.
- The Copeland EVH Series is designed for large, centralized racks (including CO2), HVAC applications, advanced chillers and industrial refrigeration applications.
Learn more about applying our VFD solutions to your HVACR operations by visiting our webpage.
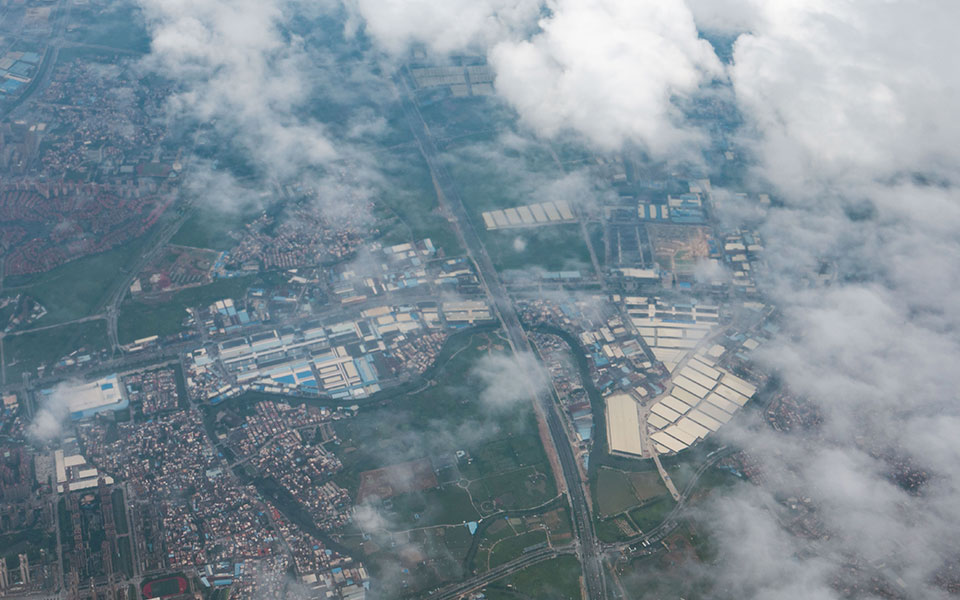
Industrial Heat Pumps Deliver Sustainability, Lifecycle Benefits in Food and Beverage Industry
by Grant Kovac | Solutions Spotlight
The food and beverage industry faces increasing pressure to reduce scope 1, 2 and 3 emissions. In...
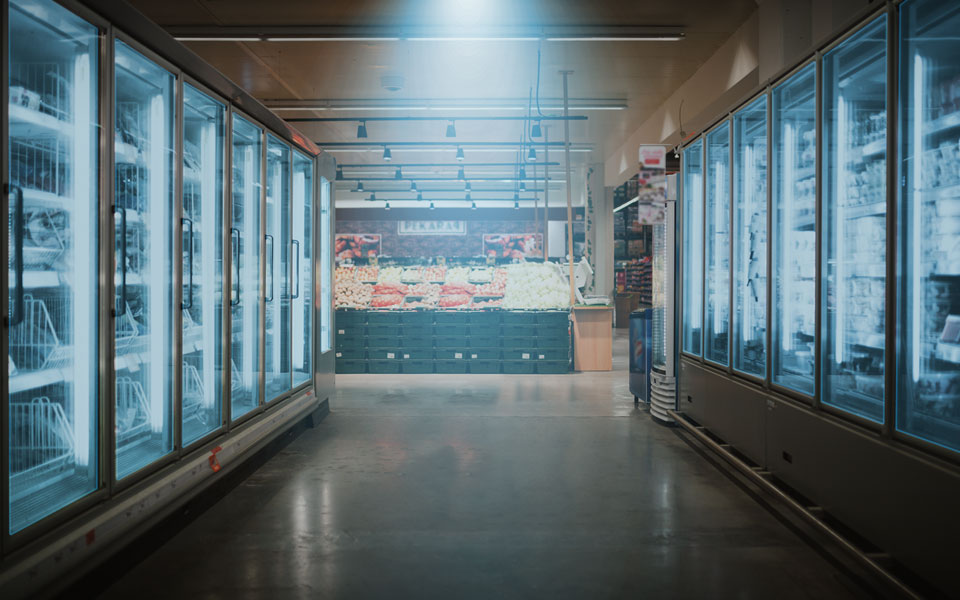
10 Innovations Transforming Retail Operations
by Andre Patenaude | Solutions Spotlight
*On June 1, 2023 Emerson’s Climate Technologies business became a new standalone company –...
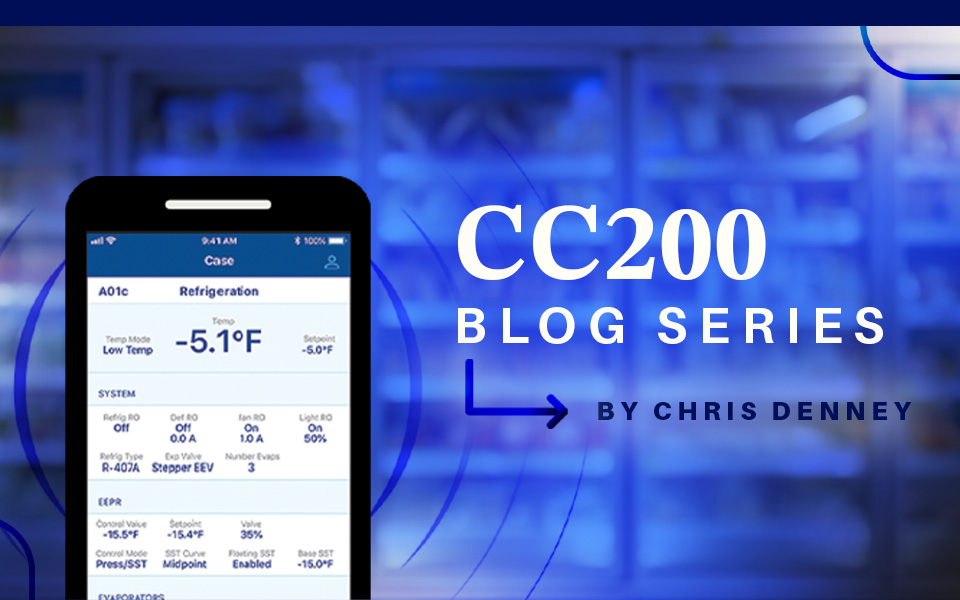
Simplify Refrigerated Case Servicing and Troubleshooting
by Chris Denney | Solutions Spotlight
*On June 1, 2023 Emerson’s Climate Technologies business became a new standalone company –...
The post Optimize Supermarket Energy Efficiency and Performance With VFD Retrofits appeared first on Copeland.